In 2022, Roxia is partly acquired the German-based company Aquachem. As our customer base is growing, Aquachem is very happy to announce that Client* has installed one of fully automatic AF1200. It is now filtering aluminum hydroxide from waste water that is produced during the anodization of the aluminum profiles. The fully automatic filter press, installed on a work platform, uses an automatically controlled rocker to transport around 6,500 kg of filter cake into the container below.
*The Dutch division of the company develops and manufactures extruded profiles and machined aluminum products for the construction, transport, automotive and industrial sector.
High Quality Corrosion-Resistant Materials
The company previously worked with a conventional chamber filter press, which had to be completely emptied and cleaned manually every day. Due to the use of so-called overhang filter cloths, the filter press could not be completely sealed and suspension leaked from the filter press. The solids content of this press was also only 22%.
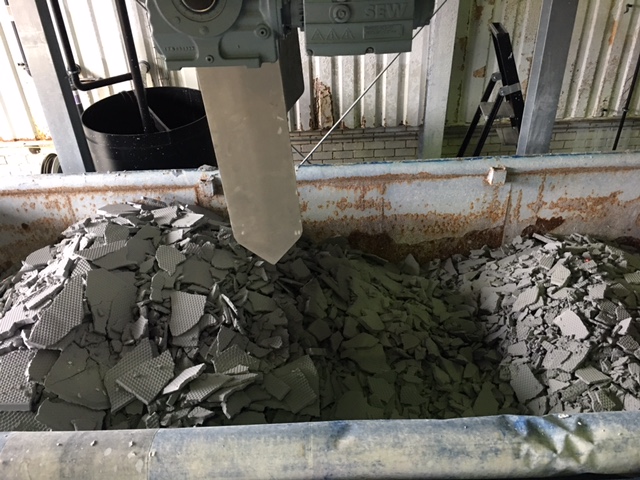
Overpressure to prevent the penetration of corrosive media
Eric Reijans, head of the surface treatment department, explains: “We chose AQUACHEM because their AF series runs fully automatically 24/7. After comparing different models and manufacturers, the AF1200 was the only machine that really works fully automatically. The compact structure and the good ROI were also important decision criteria for us.
Other filter press manufacturers build large machines that require daily cleaning. This makes the cleaning work far more extensive. With the integrated cloth washing system on the AF, cleaning is reduced to a minimum. Thanks to a good cooperation, mutual listening and the careful search for the right solutions, we were able to implement the project with the desired result. This has opened the door to a long and good cooperation that we would like to expand in the future.”.
With our fully automatic AF1200, the solids content increased from 22% to at least 33% so that more filter cake can be collected in the container. This leads to around 600 tons less waste per year. This corresponds to around 35 truckloads and not only reduces the amount of waste but also the freight costs considerably.
We are very happy about this project and even more about our satisfied customer!
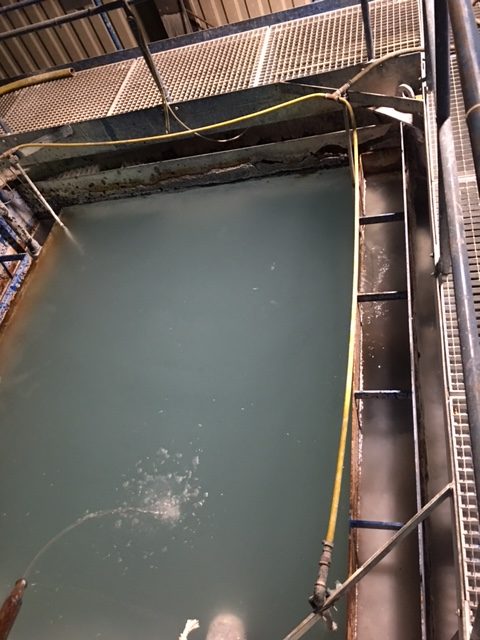